Lithium ion battery fires are extremely rare but due to the technical nature of batteries, extinguishing them is a big challenge. It is, therefore, sensible to examine the causes, counter- and preventive measures a bit more closely.
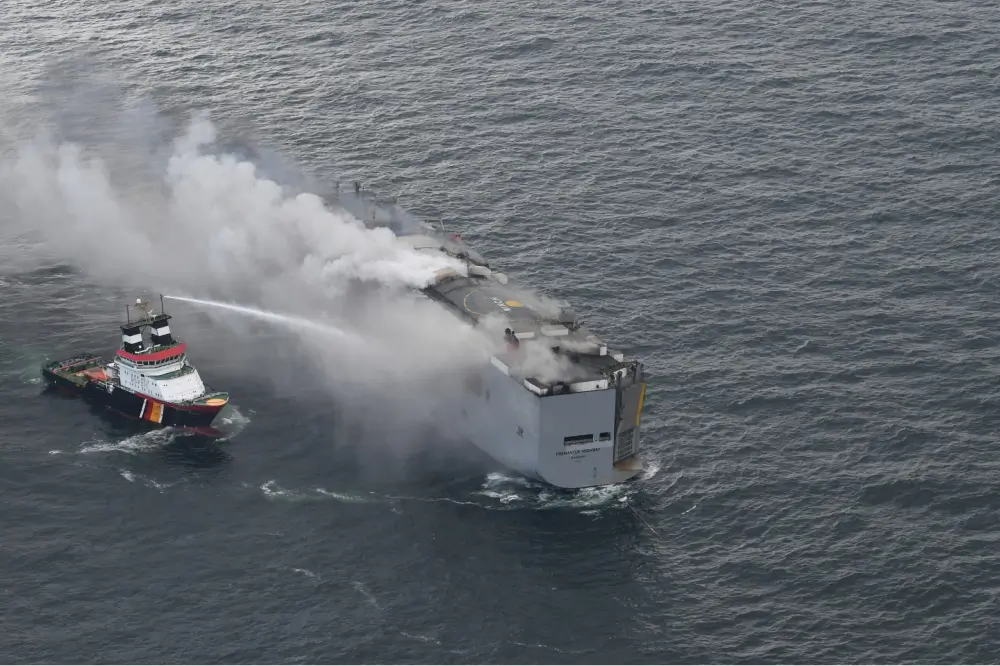
Lithium ion battery fires are extremely rare but due to the technical nature of batteries, extinguishing them is a big challenge. It is, therefore, sensible to examine the causes, counter- and preventive measures a bit more closely.
‍
While the exact circumstances are still to be determined, the pictures of a ship carrying more than 3,000 cars in the North Sea were dominating the news headlines end of July. The cause of the fire is yet to be determined. However, the theory that the fire was caused by an electric vehicle seems more and more unlikely. After the inspection of the freighter all 498 electric vehicles were found in good condition. In general, battery fires are extremely rare but due to the technical nature of batteries, extinguishing them is a big challenge. It is, therefore, sensible to examine the causes, counter- and preventive measures a bit more closely.
BMS malfunctions like over-charging or over-discharging: BMS malfunctions like sensor offsets can lead to unsafe operations. Over-charging batteries can cause excessive heat inside the battery. This heat can trigger further reactions resulting in side-reactions like electrolyte decomposition or copper dissolution, ultimately creating an internal short-circuit. Just like over-charging, high and fast discharging a battery can create the same effects.
It's also important to note that continuous over-charging can degrade the battery's health over time or cause battery swelling making it more susceptible to fires.
Physical Damage: Physical damage can take various forms such as punctures, crushes, or constant pressure on battery housing. In such situations, the physical structure of the battery is compromised. This can create internal short circuits or lithium plating at certain areas of the electrode all leading up to potential battery fires.
Manufacturing Defects & Poor Quality Control: These are flaws that occur during the battery production process. Metal particles that end up inside the battery, poor welding at the battery terminals, inconsistent electrode coating, too much silicon within the electrode experiences excessive volume expansion and inadequate quality control of the battery components are only a few examples of such defects. Additionally, poor quality control may result in the use of substandard materials or the overlooking of design flaws, both of which can lead to battery failure. For instance, a poor-quality separator may not adequately prevent the electrodes from touching each other, which can cause a short circuit and potentially a fire.
Extreme Temperatures: Batteries are designed to operate within specific temperature ranges. High temperatures can cause decomposition of the materials in the battery. This in return accelerates side reactions, creating more heat, ending up in a vicious cycle and a battery fire.
Understanding all these direct causes of battery fires and more specifically understanding where they come from already brings a lot of value and increases battery safety.
But not all safety events are happening because of the battery itself. There are lot of influences around a battery that can fail. We call it the outer circle of risk.
‍
Cooling system: The cooling system in an electric vehicle (EV) or energy storage system is designed to maintain the optimal temperature range of the battery, which is usually between 20 and 40 °C (68 and 104 °F). Most electric vehicles are equipped with a liquid cooling system. Exceeding the safe operating temperature (for a sustained period of time) due to a cooling system failure can lead to accelerated aging but also fires.
Other (safety) components: Smoke detectors and sprinklers for instance are common components within an energy storage system to prevent or extinguish fires. However, batteries do not always align well with these safety systems. If a smoke detector for instance turns on the sprinkler system, the water from these devices can cause a short circuit and thermal runaway in the battery. This applies mostly to stationary energy storage systems but also electric vehicles’ external systems such as chargers are known causes for fires.
Cable fires: Cables within a battery can be damaged, for example because of mechanical stress, for example because of extreme vehicle operation or careless maintenance. These damaged cables can overheat and, eventually, start a fire.
Accidents: An external impact on electric vehicles or energy storage systems, for example a car crash, but also incidents like wildfires can create a large enough mechanical stress on the battery to start a fire or direct short-circuit a battery.
Each of these causes can contribute to battery fires. The most common cause for battery fires, however, is the unknown. In the majority of cases battery systems are irrevocably destroyed. Conclusions on the causes of the fire are sometimes not possible anymore. This is why preventing battery fires is the most important step.
‍
Fires in electric vehicles and energy storage units are complex to handle due to the chemical composition of batteries which can sustain a fire without outside supply of oxygen. Cooling the system and waiting for the reaction to die off is the general approach.
Firefighters often use a lot of water to extinguish an electric vehicle battery fire. Lithium-ion batteries can generate intense heat when they catch fire. This heat can cause thermal runaway, a situation where one cell overheating can cause adjacent cells to overheat as well, creating a chain reaction, a so-called thermal propagation. To stop this chain reaction, firefighters cool the battery with large volumes of water. Water cools the battery pack and helps to prevent other cells from igniting.
Some fire departments might also use special foams or other extinguishing agents, but these are generally secondary to the use of water. This is because these other agents might not provide sufficient cooling to the battery pack to prevent thermal propagation.
Firefighters use thermal imaging cameras to monitor the temperature of the battery pack. This helps them to determine if the fire has been sufficiently extinguished, or if the battery is still at risk of reignition. Once the fire is extinguished, the battery needs to be continuously monitored for a significant time. Batteries can reignite hours or even days after a fire has been extinguished. Fire departments may work with the vehicle manufacturer or a towing company to ensure the safe removal and storage of a damaged battery.
Water run-off from this procedure is also a potential environmental hazard. The water can carry chemical contaminants from the fire, so firefighters need to prevent it from entering storm drains or bodies of water. In the case of the freight ship in the North Sea, water poses the additional risk of sinking the ship. By hosing down the sidewalls with water, they try to cool down the ship without sinking it. Yet, the difficulty in putting out fires on ships is a more general challenge and not linked to electric vehicles as a recent incident in New Jersey shows.
In all scenarios, the most effective strategy against electric vehicle and energy storage system fires is prevention. This includes proper design, sourcing, installation, maintenance, and monitoring of these systems to ensure early detection and mitigation of any faults that could lead to a fire. Users should also be educated about safe practices and potential hazards associated with the misuse of these systems.
‍
A preventative safety solution for batteries should cover both circles of risk, the inner and the outer, building two lines of defense.
Good design: Good design plays a critical role in the prevention of battery fires. It starts by selecting the best battery cell, BMS and system design that withstand varying operating conditions and stresses. The design should also ensure the secure containment of battery components, particularly the electrolyte, which is flammable.
Additionally, the architecture of battery packs, especially in electric vehicles or energy storage systems, should be designed to isolate failures and prevent a single cell's malfunction from affecting others (thermal propagation), thus reducing the risk of a larger-scale fire. Incorporating robust thermal management systems in the design can also ensure effective heat dissipation and prevent overheating.
Thorough Quality Assurance: An essential preventive measure against battery fires lies in thorough quality assurance during the manufacturing of battery systems, from cell production to final installation. Strict limits in initial and end-of-line tests result in a higher rejection rate but are necessary to rule out future malfunctions as far as possible. Faults that are not detected directly must be identified as early as possible.
Early detection of defects: Continuous monitoring of batteries is vital. Any anomalies detected should trigger a warning or, if necessary, shut down the system to prevent further damage. The use of advanced diagnostic tools and techniques can help identify potential problems early on, even before they can lead to noticeable performance issues. The earlier battery teams are informed about potential defects, the better.
An early detection gives battery teams the opportunity to take appropriate preventive action. Battery analytics software for example can detect anomalies in the system, that can be classified into different risk levels, providing a second layer of safety, and enabling timely replacement. Regular inspections and maintenance can also contribute to early defect detection. For example, physical signs of battery damage, such as swelling or leakage, can indicate an internal problem.
Identification of potential causes for thermal runaways: Another crucial aspect of preventing battery fires is the early identification of potential causes for thermal runaway. Effective battery management systems (BMS) are vital in this regard. These systems monitor and control the battery's operating conditions, including charge levels and temperatures, and can intervene when abnormal conditions are detected. For example, the BMS can prevent overcharging or discharging and can disconnect the battery if temperatures exceed safe levels.
Beyond that battery analytics can provide a second layer of safety, early on detecting indicators for deteriorating battery conditions and causes for thermal runaways, e.g., lithium plating. Regular inspection and maintenance of batteries can also help identify signs of potential problems, such as swelling or leakage, which can indicate a risk of thermal runaway. Understanding the signs of impending thermal runaway and acting promptly can effectively mitigate the risk of battery fires.
While no safety measure can guarantee 100% protection, the more causes can be detected the fewer fires will start. Battery fires, while relatively rare, can cause serious harm. By understanding the causes, counter- and preventive measures, we can all contribute to a safer battery-powered world.
‍
(photo source:Â kustwachtvliegtuig)
Sign up for the next live group demo and learn how TWAICE can transform your BESS operations. In just 30 minutes, you’ll get a demo of key features and use cases, and engage with our product experts for a live Q&A.